In a recent announcement from the Department of Health and Social Care Health Minister Edward Argar discussed government plans to explore the recycling of pandemic-related PPE plastic waste into new products, ranging from curtains and mattress covers, to the many other healthcare products used daily across hospitals and clinics in the UK. In addition to this, Minister Argar stated that NHS Test and Trace was “exploring alternatives to current test devices” which would be “safe, effective and made of predominantly recyclable or biodegradable materials” in an effort to curb the UK’s pandemic related plastic waste.
Having previously delved into the world of facemask recycling with our ‘3D Printing with recycled facemasks project’, Minister Argar’s comments got us thinking… could we turn our old acquaintance, the Type IIR Polypropylene Facemask into casings for Lateral Flow Tests?
Inevitably, this line of enquiry proved to be quite the digression from my PhD research, involving injection moulding machines, 3D printed mould tools and many other things that are detailed in the following sections.
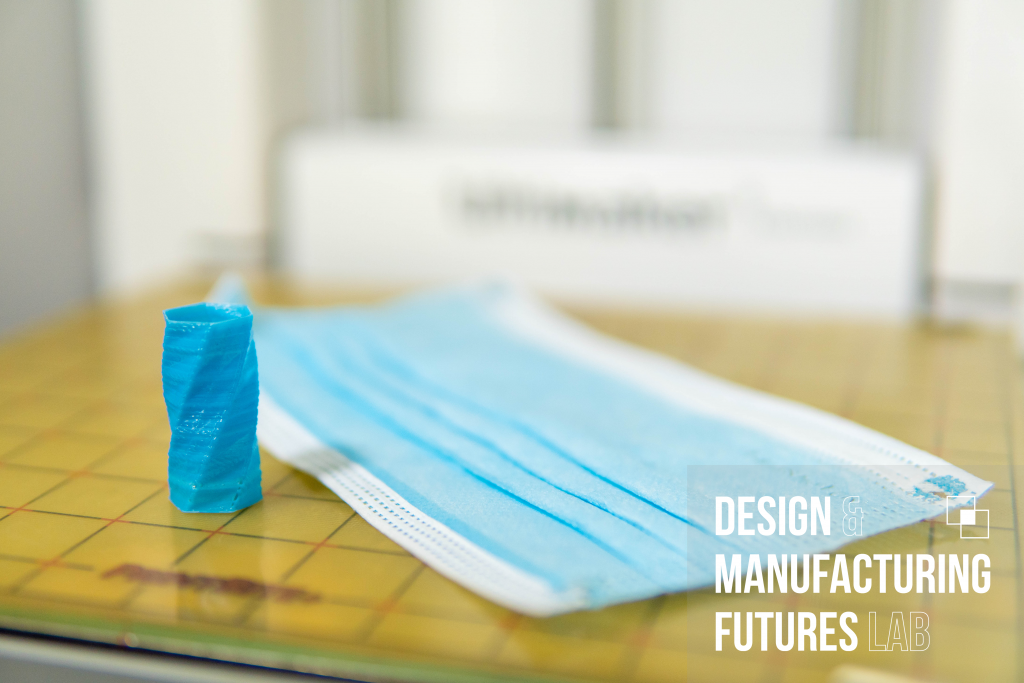
TLDR: Injection moulding with recycled Polypropylene facemasks could potentially be viable, particularly for low cost prototyping. Also, 3D printed mould tools work pretty well and worth having a look at if you get the chance.
Pre-processing type IIR Facemasks (Polypropylene)
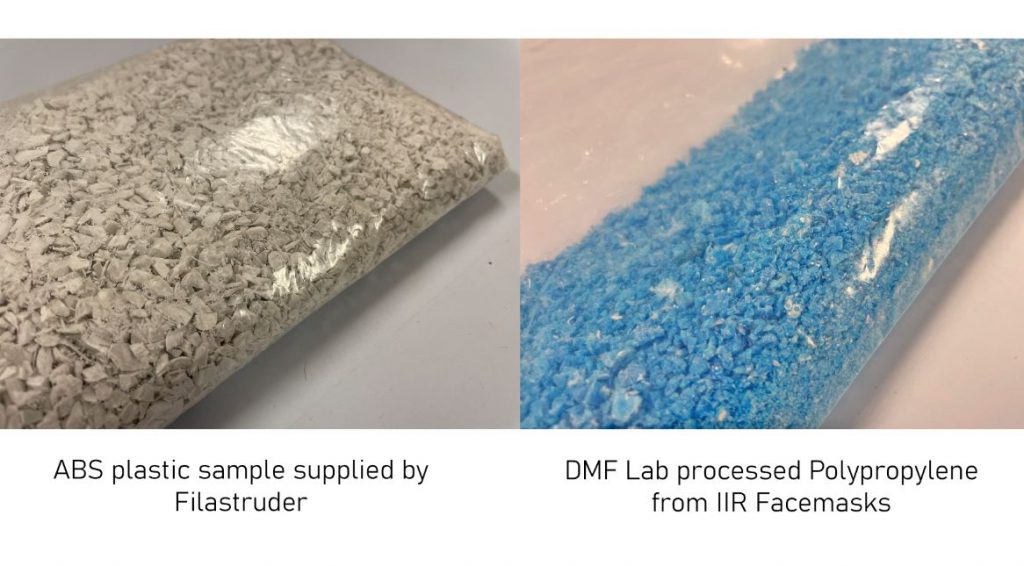
As with the 3D printing facemask project, the first step is to pre-process the masks into something easier to work with and conforms to the requirements of the moulding machine (or close enough).
For more information on pre-processing check out our previous post where you can find details on turning masks into a pelletised form for thermoforming.
Process Overview
Whilst 3D Printing has its benefits, speed is often not considered one of them. For example, to print a complete LFT case would take about 2 hours on a conventional desktop 3D printer. With over 1 million tests used a week in the UK, meeting such demand with 3D Printing could be a challenge. Considering this, we decided to look into the process currently manufacturing the unprecedented volumes of LFT cases, Injection Moulding.
Steps
- Designing the LFT case and mould tools
- Manufacturing the moulds
- Injection moulding parts with recycled facemasks
Warning: Attempt to read property "post_type" on null in /bitnami/wordpress/wp-content/plugins/elementor/includes/utils.php on line 927
Warning: Attempt to read property "post_status" on null in /bitnami/wordpress/wp-content/plugins/elementor/includes/utils.php on line 933
Warning: Attempt to read property "post_status" on null in /bitnami/wordpress/wp-content/plugins/elementor/includes/utils.php on line 936
Warning: Attempt to read property "ID" on null in /bitnami/wordpress/wp-content/plugins/elementor/includes/utils.php on line 937
Notice: Function map_meta_cap was called incorrectly. When checking for the
edit_post
capability, you must always check it against a specific post. Please see Debugging in WordPress for more information. (This message was added in version 6.1.0.) in /opt/bitnami/wordpress/wp-includes/functions.php on line 6114Warning: Attempt to read property "ID" on null in /bitnami/wordpress/wp-content/plugins/elementor/includes/utils.php on line 939
Warning: Attempt to read property "post_type" on null in /bitnami/wordpress/wp-content/plugins/elementor/includes/utils.php on line 927
Warning: Attempt to read property "post_status" on null in /bitnami/wordpress/wp-content/plugins/elementor/includes/utils.php on line 933
Warning: Attempt to read property "post_status" on null in /bitnami/wordpress/wp-content/plugins/elementor/includes/utils.php on line 936
Warning: Attempt to read property "ID" on null in /bitnami/wordpress/wp-content/plugins/elementor/includes/utils.php on line 937
Notice: Function map_meta_cap was called incorrectly. When checking for the
edit_post
capability, you must always check it against a specific post. Please see Debugging in WordPress for more information. (This message was added in version 6.1.0.) in /opt/bitnami/wordpress/wp-includes/functions.php on line 6114Warning: Attempt to read property "ID" on null in /bitnami/wordpress/wp-content/plugins/elementor/includes/utils.php on line 939
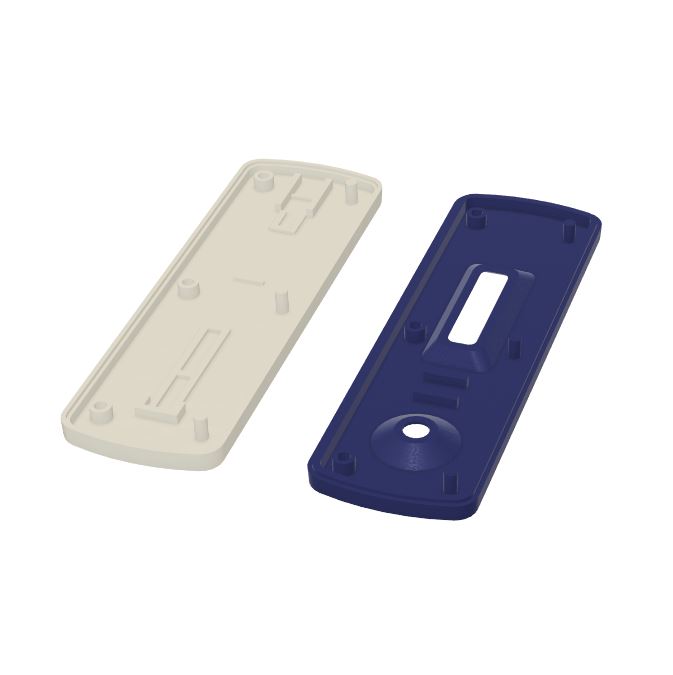
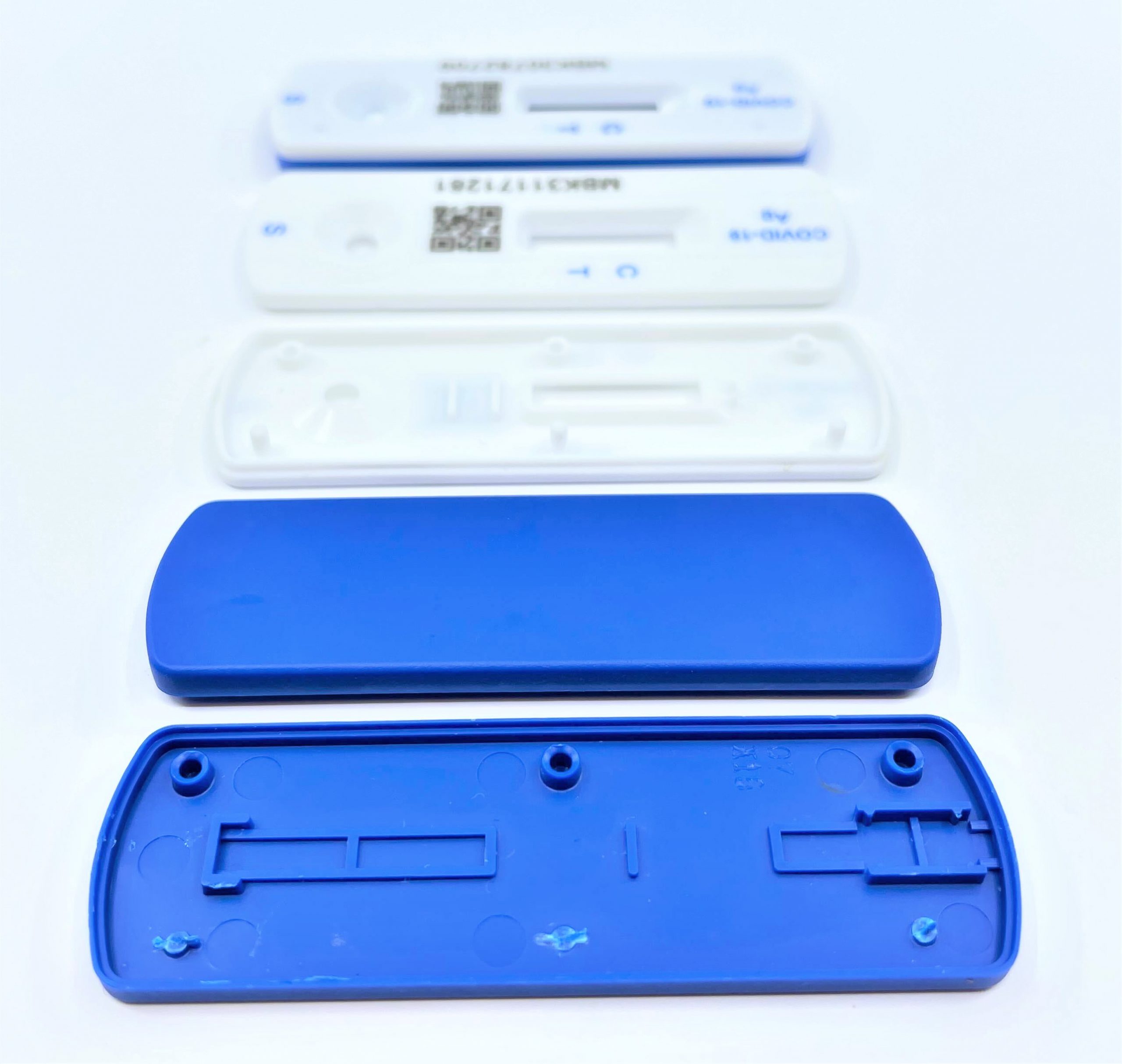
Mould Modelling and Simulation
A Computer Aided Design (CAD) model was developed to capture key case geometry and surface detail after reverse engineering the standard issue LFT casing. The CAD model was further used to generate core and cavity style mould tools. Where traditionally mould tools are machined from tool grade materials such as carbon steels or aluminium on a CNC or EDM machine, recent advances in 3D Printing materials have enabled the manufacturing of low volume tools (<100 parts) at a fraction of the time and cost. With this in mind, the tools were designed for 3D printing to include built in fixtures.
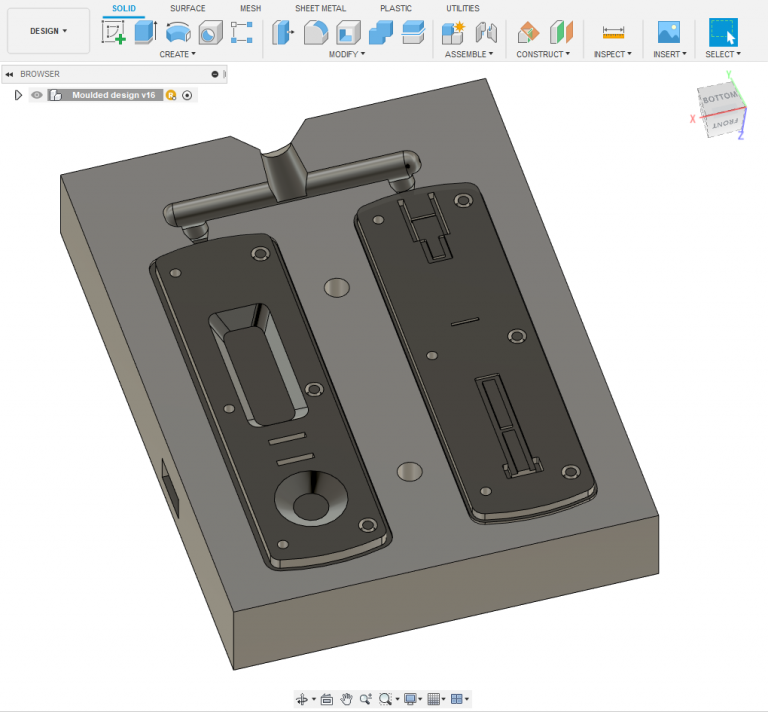
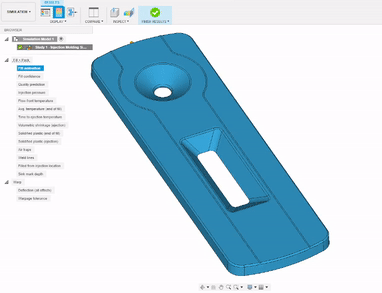
The LFT moulds were designed and simulated in the Autodesk Fusion360 CAD package. Fusion’s built in tools allow for injection moulding simulations to be performed before sending parts off to be made; providing useful info on shape suitability, estimated part quality and statistics for filling. The GIF above shows a mould filling simulation for the LFT case.
(Here’s a video to get you started with mould design in Fusion if you’re interested).
Additively Manufacturing Mould Tools with SLA Technology
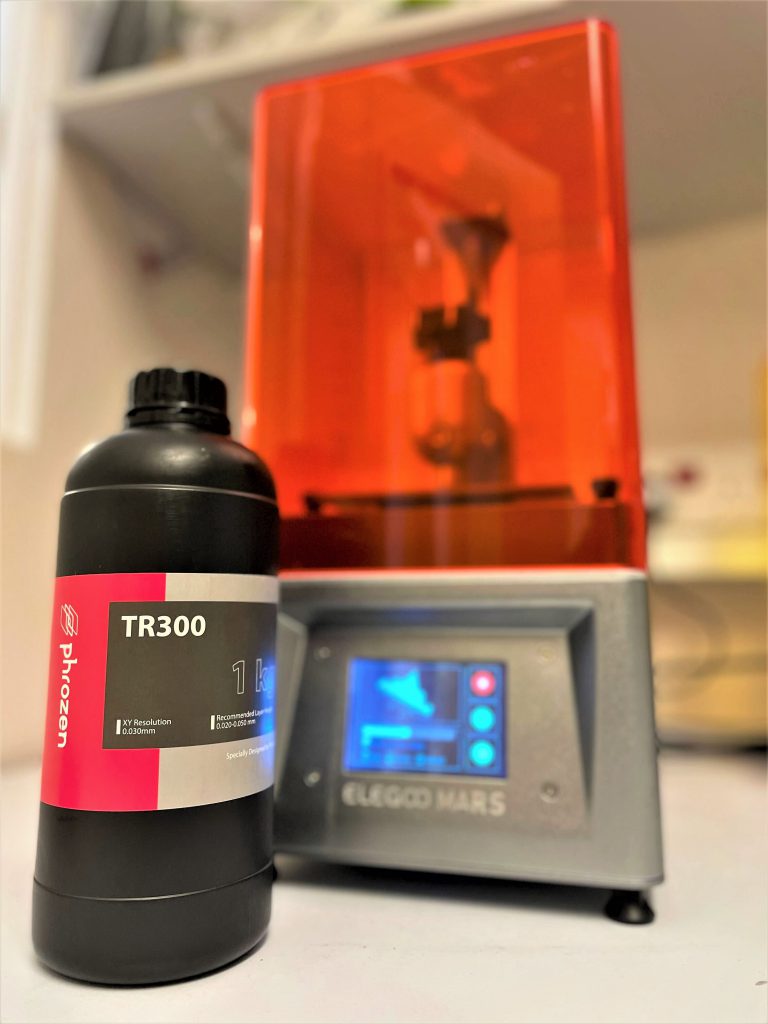
After washing and curing the printed tools (pictured right) minimal additional finishing was required, surfaces were both smooth and of reasonably high quality for a printed tool.
Print stats
- Cavity(right): 10h 33 mins, £7.96 in resin
- Core(left): 10h 51 mins, £9.17
- Total : 21h 24 mins, £17.13
Note: prints were offset from the bed and angled to avoid warping.
(Resin settings for mars: ET 10s, ETB 40s – the rest are the same as the TR300 data sheet)
With tools designed and STL files in hand we enlisted the help of an MSLA Elegoo Mars 3D Printer to manufacture the LFT case tools. Whilst the mars is a fairly entry level machine (costing under £150) it is capable of reproducing incredibly fine detail, making it ideal for small scale, low cost applications.
Elegoo Mars spec:
- XY Resolution: 0.047 mm (2560*1440)
- Z Axis Accuracy: 0.00125 mm
- Layer Thickness: 0.01 to 0.2 mm
- Printing Speed: 22.5 mm/h
- Build Volume: 120 x 68 x 155 mm
The Mars printer was paired with a thermally resistant engineering resin. Manufactured by Phrozen, the TR300 resin features a heat deflection temperature of 325 °C, high tensile strength and low shrinkage. At £70/Litre the TR300 looked promising.
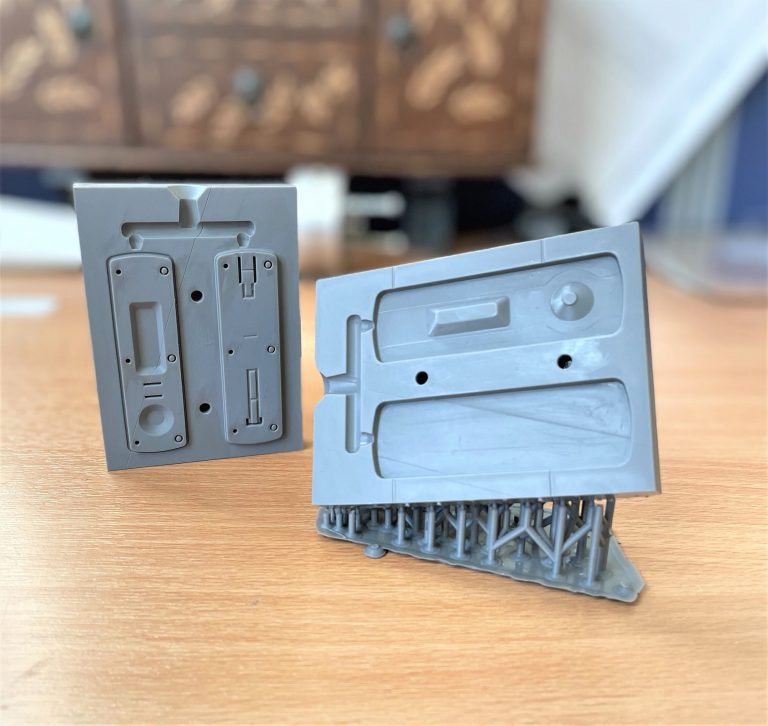
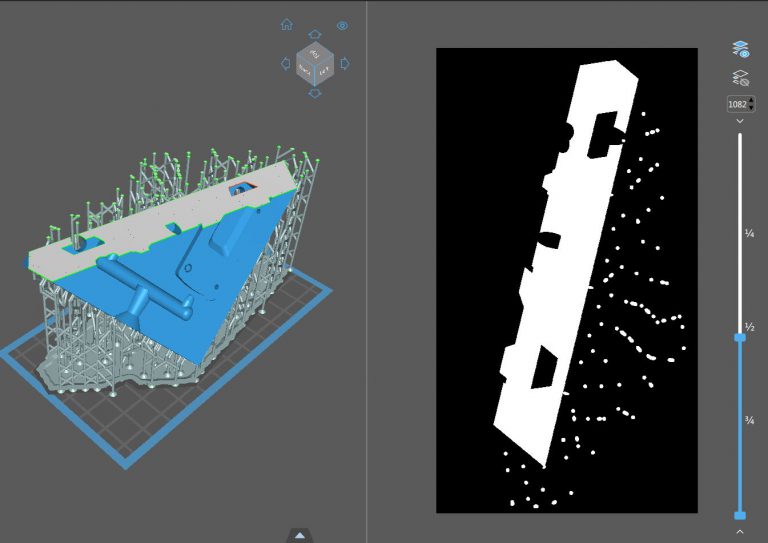
Desktop Injection Moulding
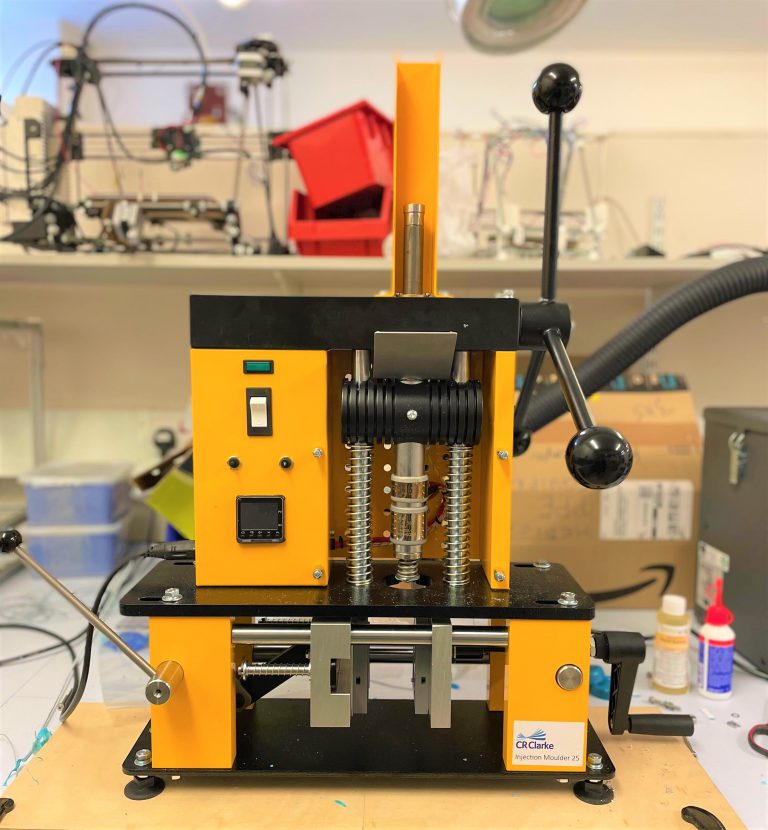
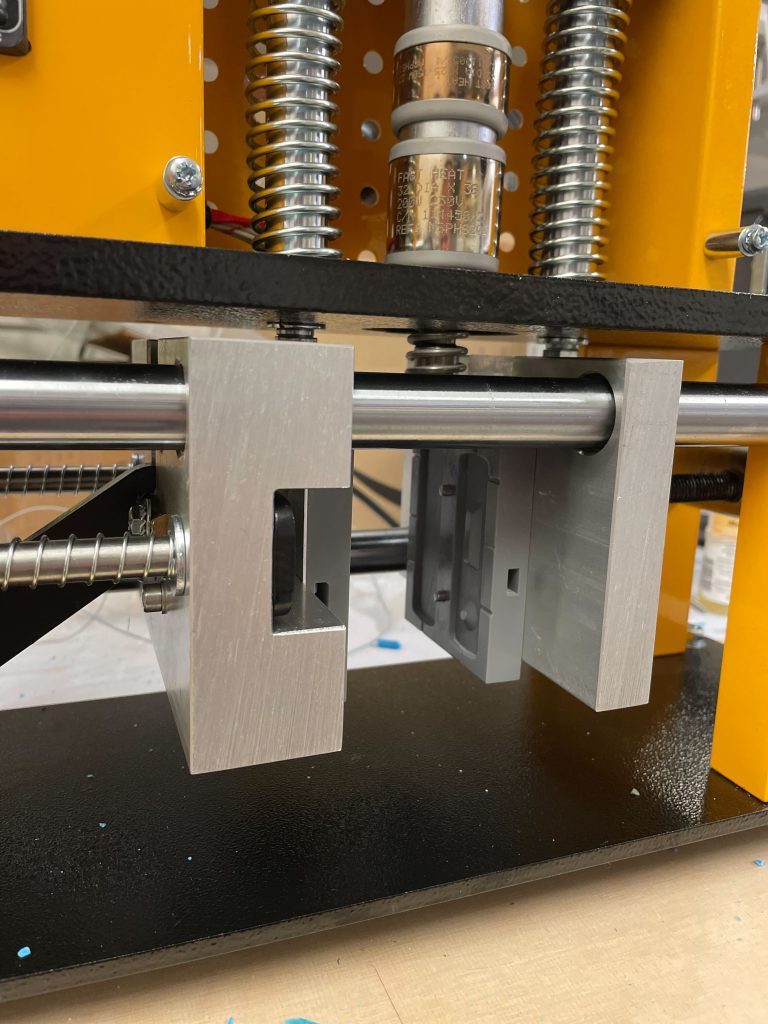
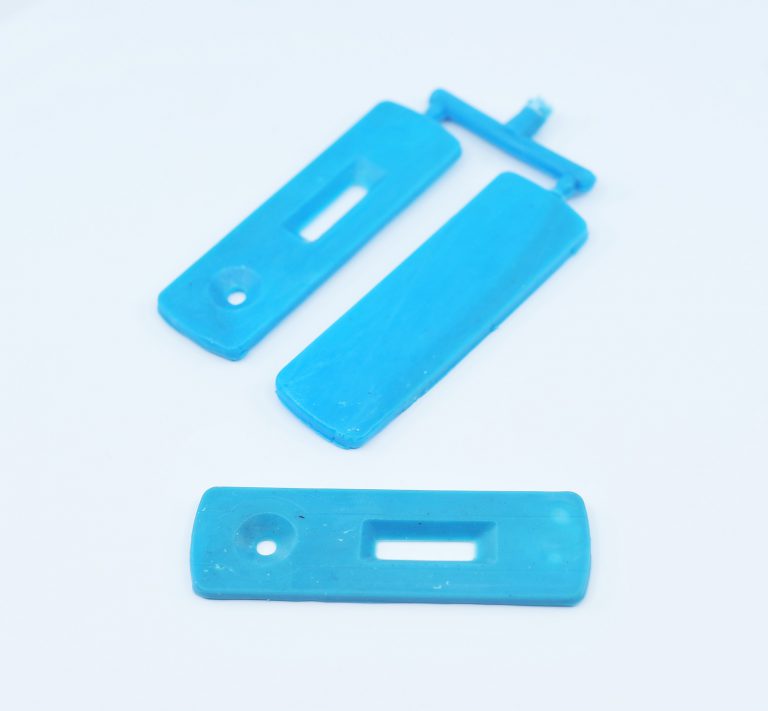
The injection moulding process involves injecting a volume of molten material into a mould over a controlled period of time. Naturally, this requires the use of a machine designed for such a task.
Pictured right is the C R Clarke 25 mechanical desktop Injection moulding machine used to mould our recycled facemasks into new, blue, LFT cases. The process itself is fairly simple. PP facemask pellets are fed into the hopper, moulds are clamped, and a user slowly, or quickly, turns a large handle until the mould cavity is filled. Here’s a good video to demonstrate.
Moulding Machine Spec
- Mould Diameter: 75 mm
- Max Mould Thickness: 95 mm
- Max Moulding Weight: 20 g
- Typical Cycle Time: 45 s
- Max Temp: 200 °C
Results
The outcome is far better than expected. Of course it could do with some refinement; fine internal details could be modified to facilitate moulding with mechanical machines, or improvements made to the mould design itself. However, it is a functional LFT case, made from recycled facemasks, using 3D Printed tools, on a desktop moulding machine.
If you would like to hear more about this project or are interested in getting involved feel free to get in touch!
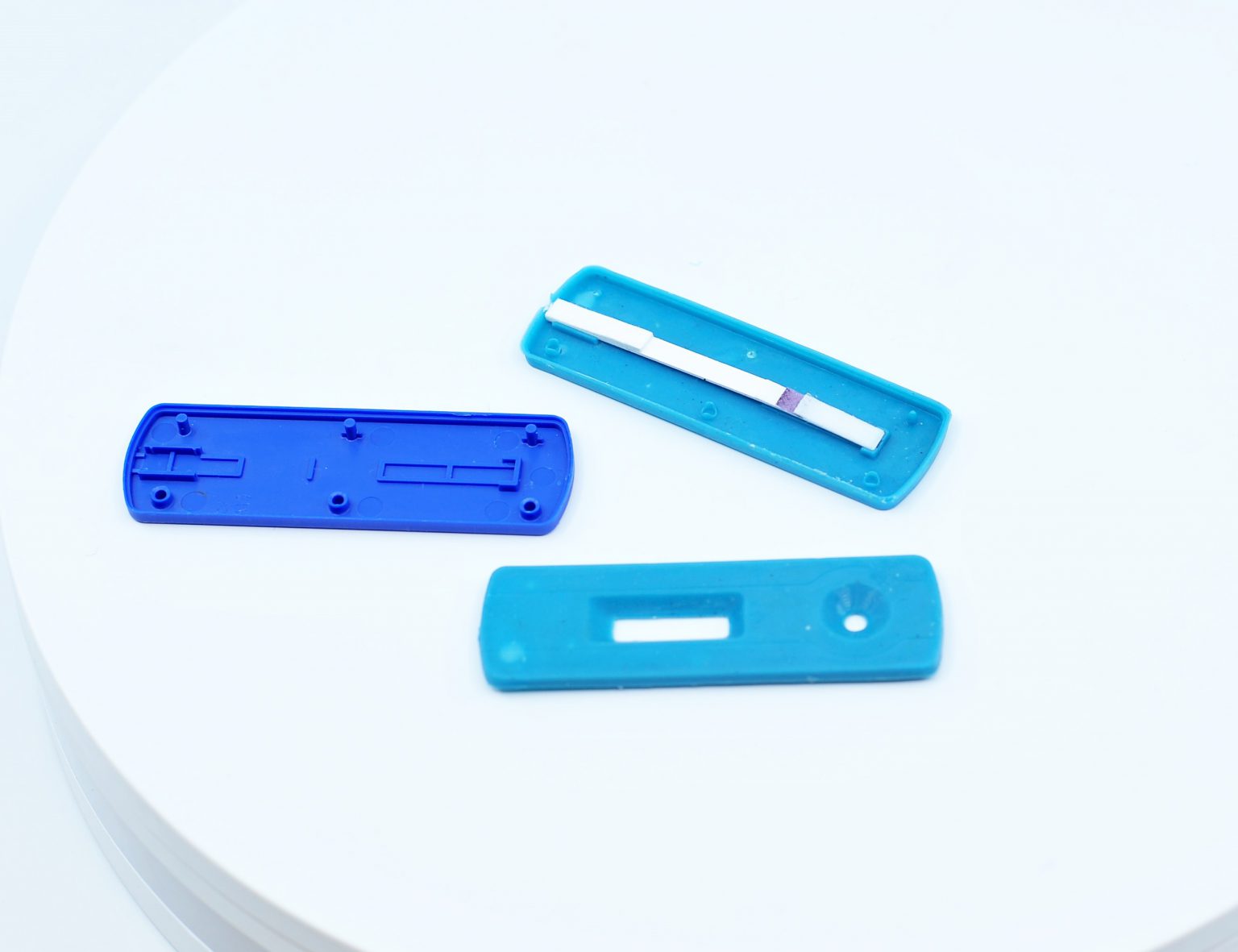
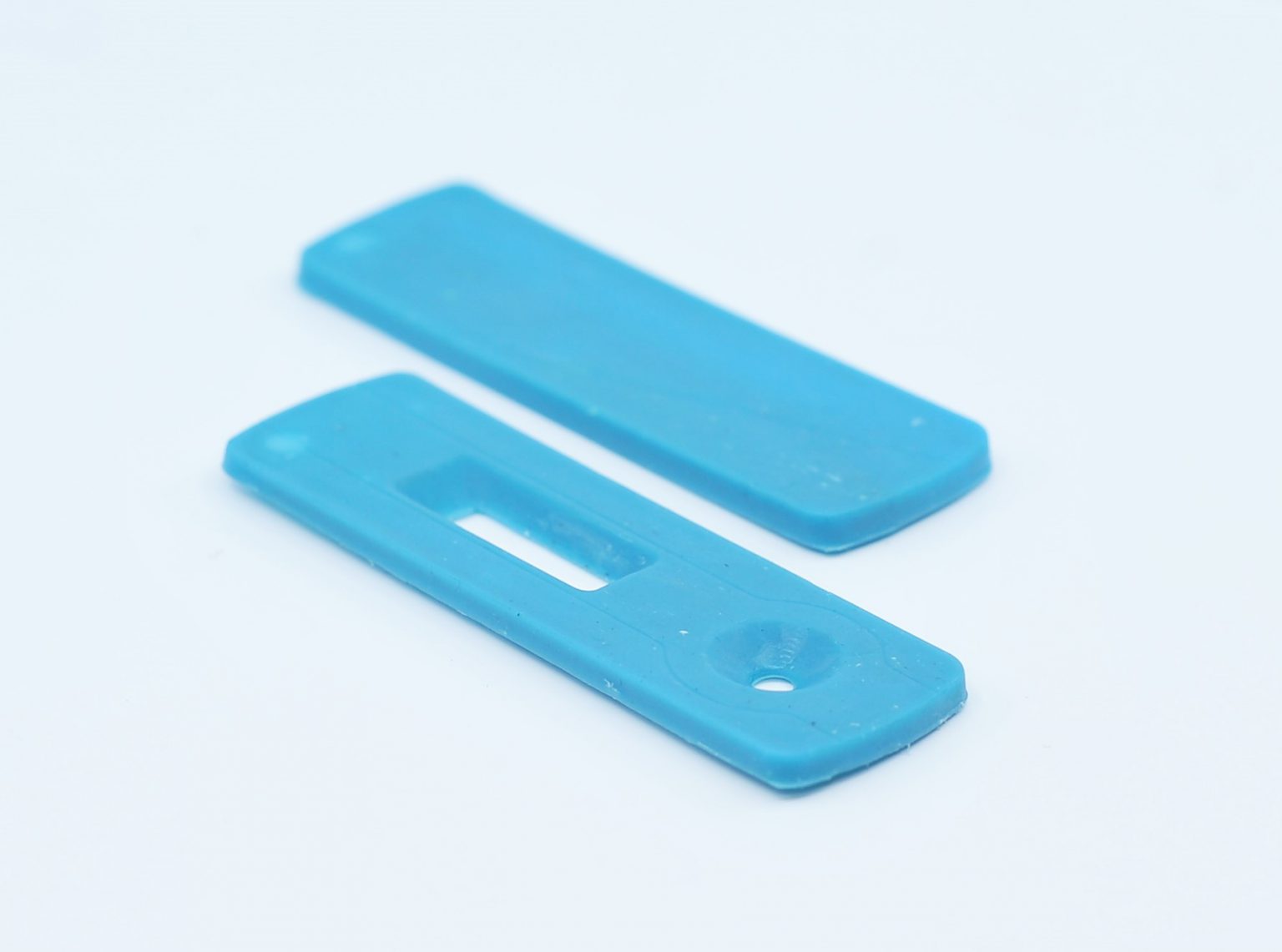
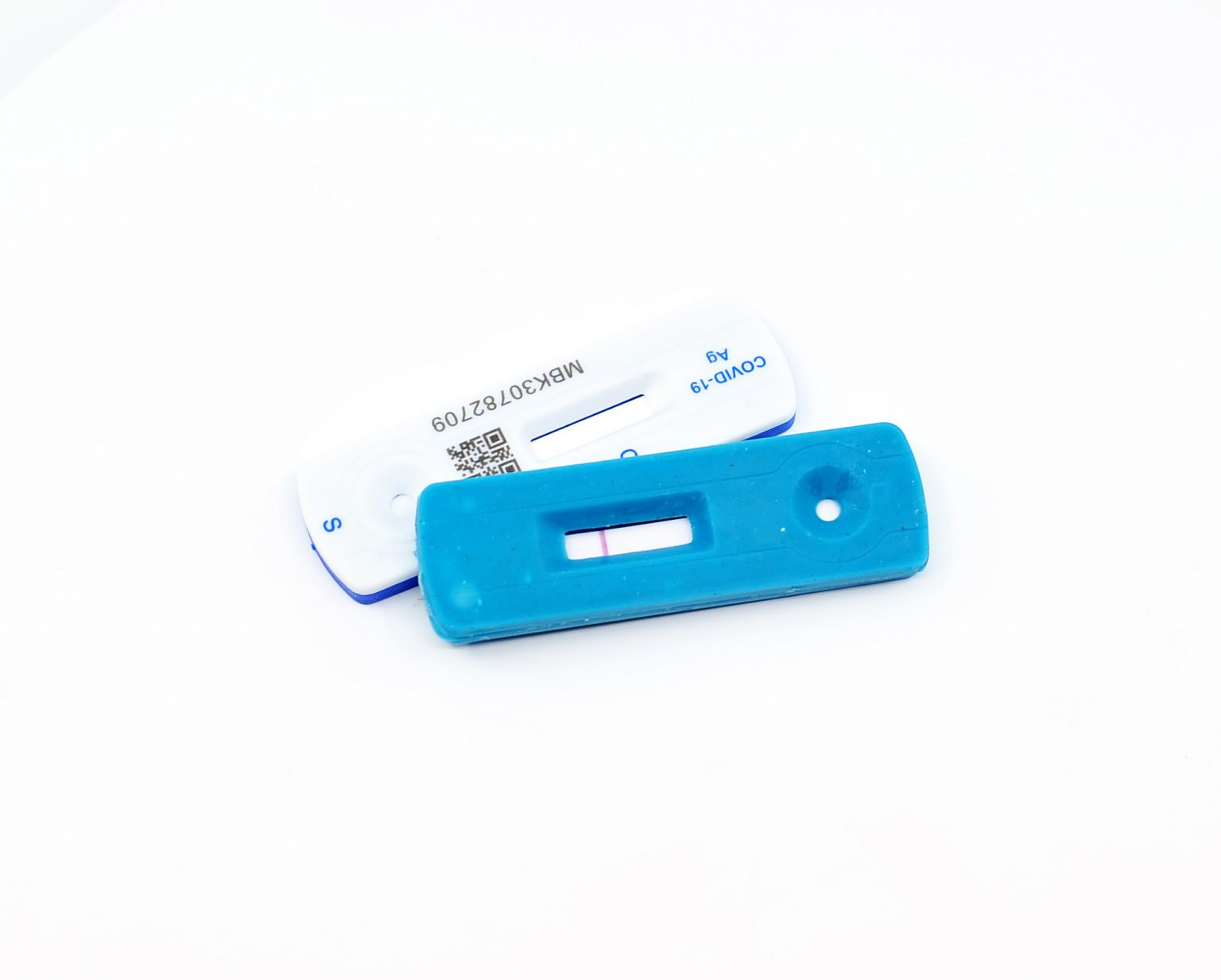
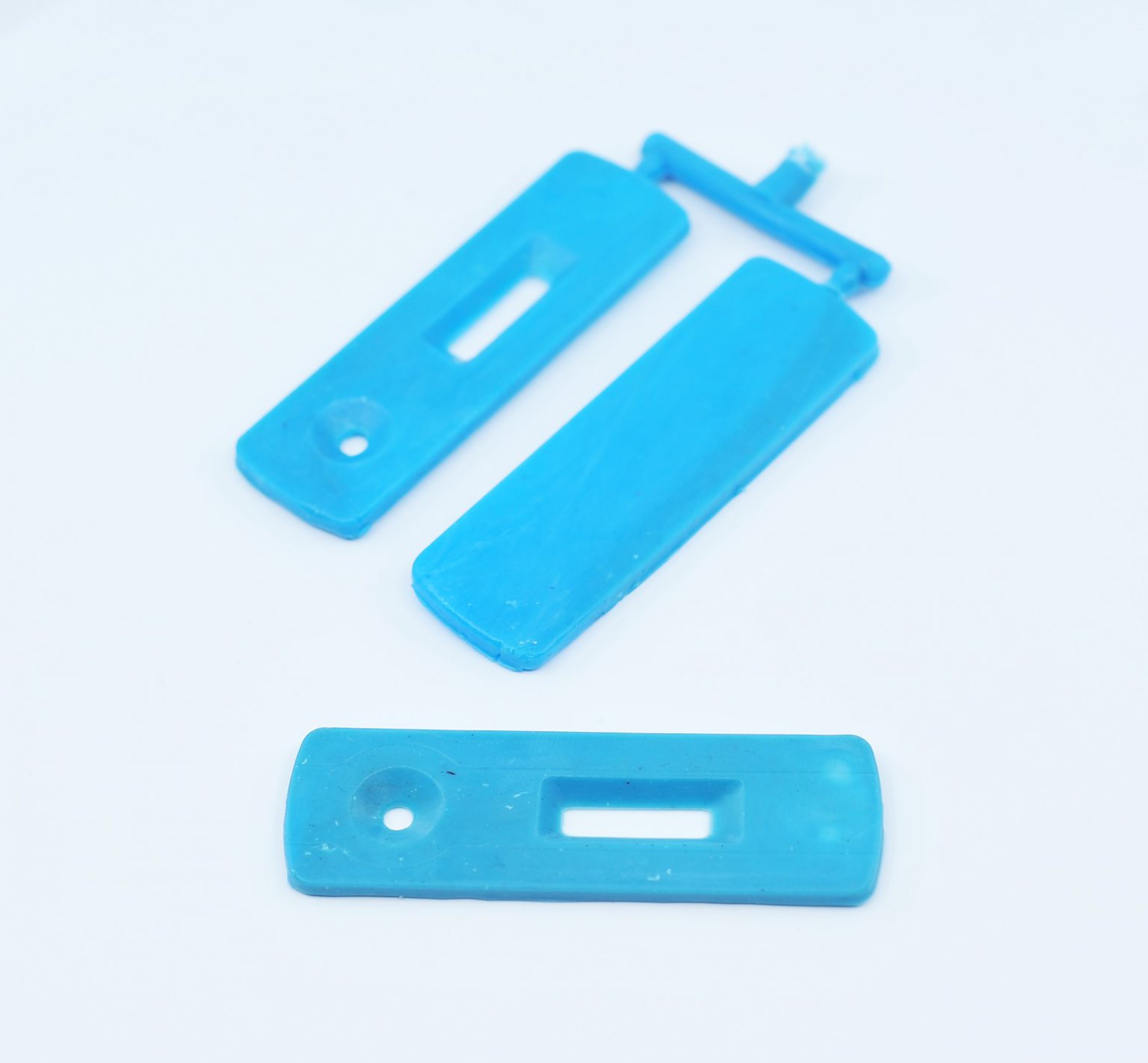
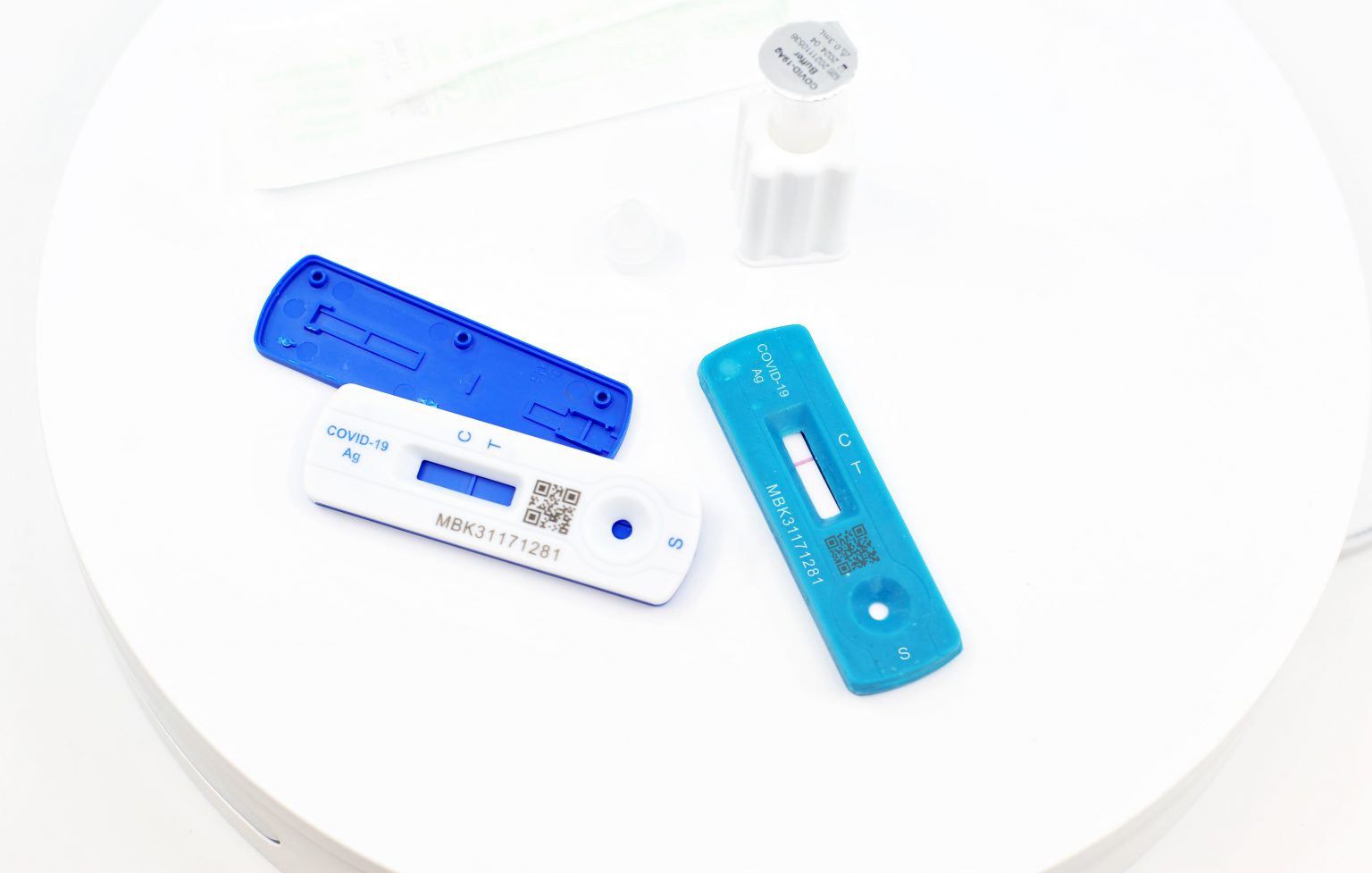
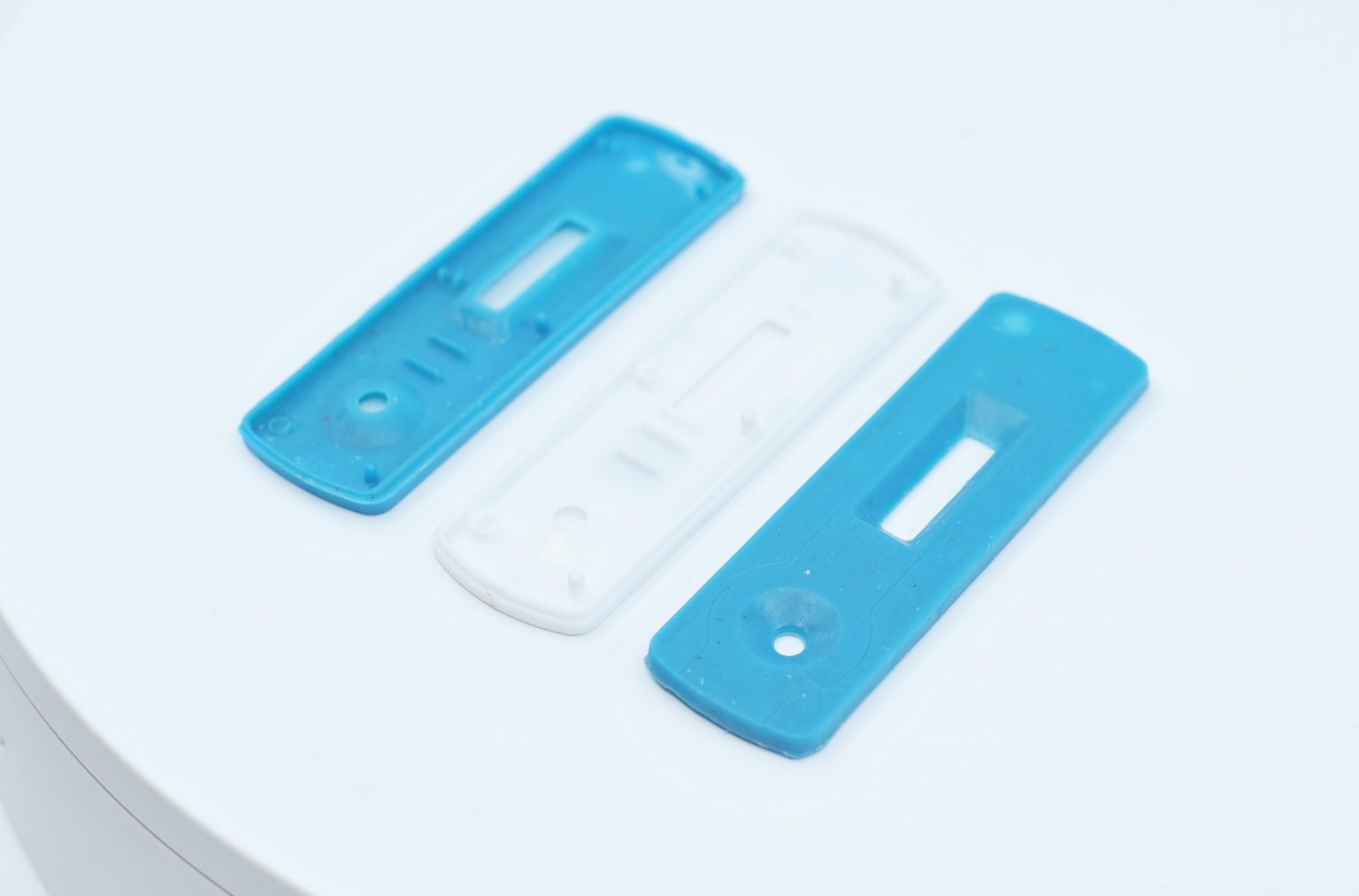
Acknowledgements
Royal Academy of Engineering for funding this work under the Project Clean Access (PCA) grant, Autodesk for their continued support and interest in our projects, Hardshell UK for supplying the masks, C R Clarke for the moulding machine, and finally my supervisors and DMF Lab colleagues.