Adam McClenaghan, David Suo, James Gopsill and Aydin Nassehi headed to Cranfield University at CIRP DESIGN 2024. David presented his work on the data and information flows through a Digital Twin, Aydin was a keynote presenter on the definition of the Digital Twin and Adam and James presented on the concept of Design for Many Manufacture.
It was a great event with lots of interesting and engaging discussions on the future of design. We look forward to attending again in the future. The papers published were:
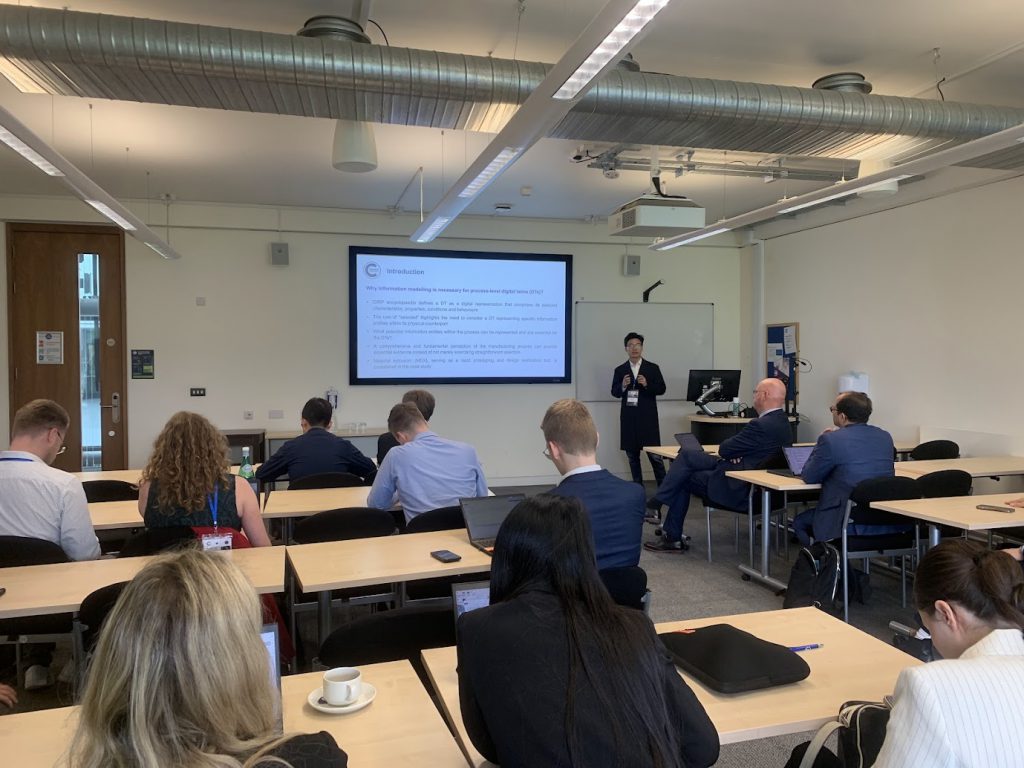
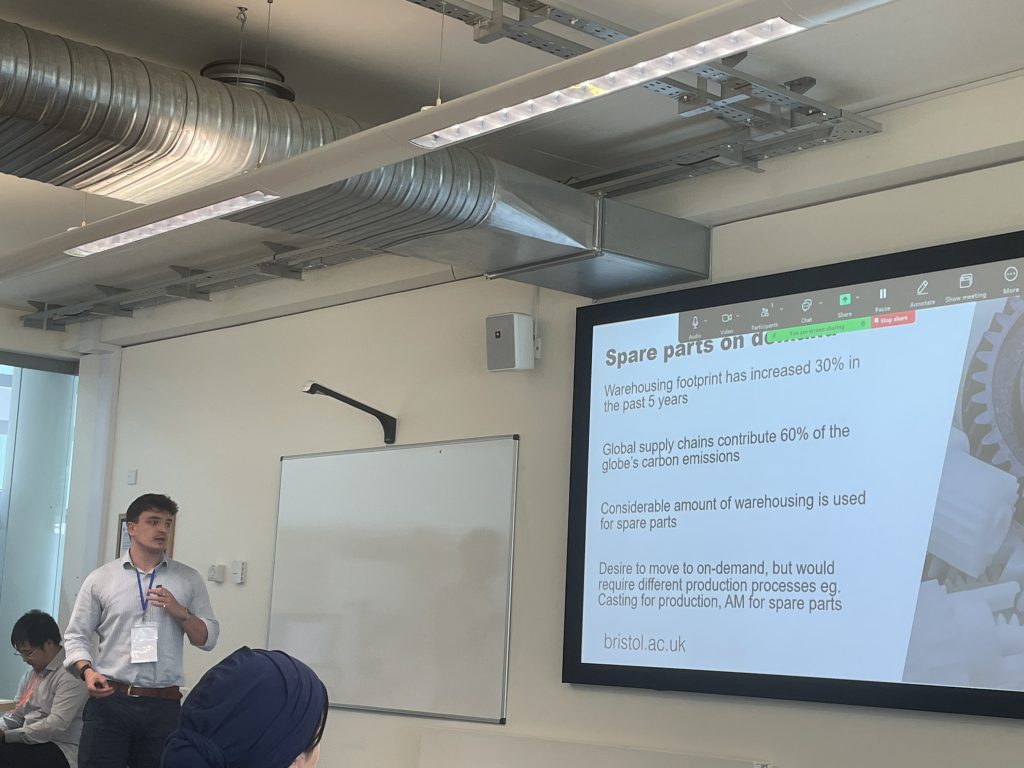
Title
Examining the trade-offs in generating designs for many manufacture.
Abstract
Design for Many Manufacture (DfM2) is a concept driven by the need to overcome supply chain issues and perform through-life maintenance to extend product lives. The premise is to design a component that can be manufactured a variety of ways and still offer the desired performance and operating characteristics. The advent of generative design and computer-aided manufacture now provides the capability to evaluate designs against many different manufacturing techniques and within a reasonable timeframe. However, designing for many manufacture has trade-offs in terms of: (1) having singular or variant designs for the many manufacturing methods; (2) definitng the set of permissible materials, manufacturing methods, and costs; and, (3) the ultimate performance of the component. This paper contributes to the field of DfM2 through an exploratory trade-off study that used generative design to create a series of components with varying load scenarios and different manufacturing constraints.
The trade-off study revealed the sensitivity of generative component designs relative to the manufacturing constraints and loading paths placed on the component, and that it remains a challenge to configure and operate a generative design task across multiple manufacturing processes. In particular, it appears the combination of constraints prevents the algorithm in identifying the ‘next best’ move and it therefore struggles to navigate the design space to find an optimal solution. The paper also suggests where and when it is suitable to consider a single design across many manufacturing processes vs. individual designs for each manufacturing process.
Title
Information Modelling of Extrusion-based 3D Printing Process for Digital Twins
Abstract
This paper focuses on the information modelling of the extrusion-based 3D printing process. It aims to facilitate the creation and management of a digital twin (DT) through a comprehensive understanding of the manufacturing process. The workflow of extrusion-based 3D printing, spanning from the CAD model to the printed part, is analysed and modelled using the Integration Definition for Process Modelling 0 (IDEF0) method. Building upon the IDEF0 model and relevant literature, a Petri net is developed to identify specific information and logic inherent to the printing process. The identified elements are subsequently filtered by the specific purpose of the DT and categorized into three classes: Component, Activity, and Property. Specifically, this study explores the material extrusion (MEX) process as implemented by the Prusa i3 MK3 printer. Derived from functional flow block diagrams and mathematical formulas, the information model consists of 21 components, 25 activities and 83 properties. This model can be considered as an information repository, which enables DTs to consider, select and synchronise specific physical information elements in their digital representation within the context of the MEX process.