Emulating Mass Properties With 3D Printing
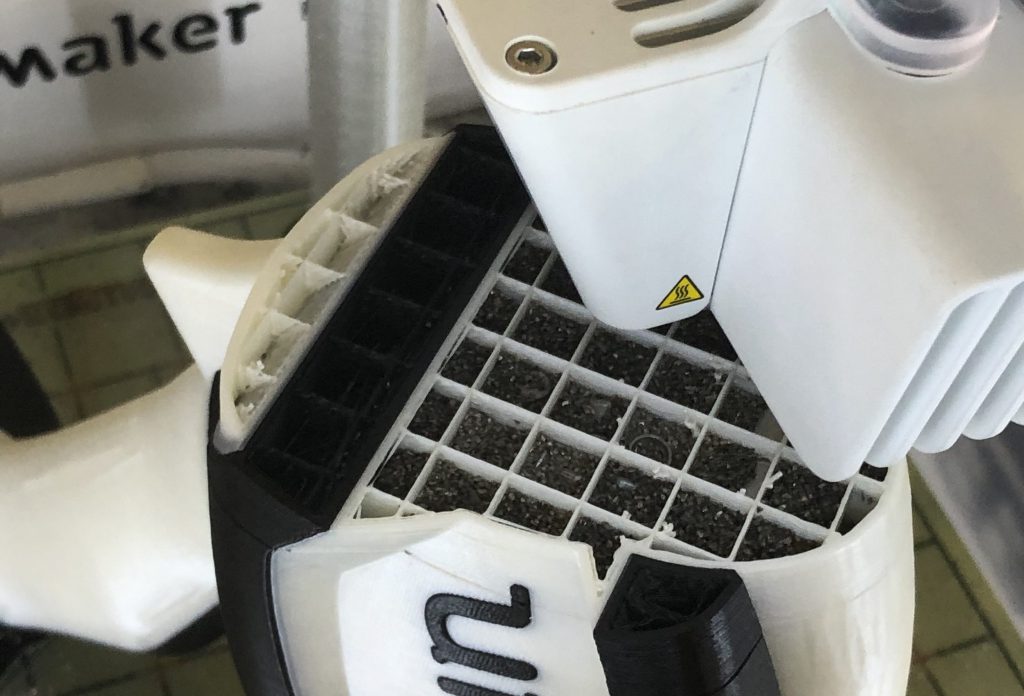
When 3D printing products it is common for the fabricated component to have significantly different mass properties to the as-designed product. This is especially true in early-stage design prototype fabrication, where understanding the geometric form of a prototype leads to rapid production of the artefact. There are several reasons for this, but the main three are:
- Neglecting to include internal components when generating a geometric representation of the external shell,
- Using a lower density thermoplastic rather than the designed-for material, and,
- Using a low-density infill pattern to save on material/production costs and time.
For some applications, this may not be important, however, it is common for stakeholders to interact with early-stage products to understand feel. Inevitably, the mass properties an artefact exhibits changes the perceived feel – with the force and torque required for interaction being directly linked to the product’s mass properties. As such, it is hypothesised that a method through which mass properties can be emulated in 3D printed products would be desirable.
This work demonstrates a methodology (presented below) through which product mass properties can be emulated using a standard 3D printing process (FDM/MEX/FFF) and machine. Written in Python, the code is able to produce a cellwise breakdown highlighting where mass needs to be placed to best emulate the desired mass properties. Work is currently continuing to slice a set of example products ready for 3D printing.

Initial results have been promising, with several case studies considered. The results from two of these – a Nintendo Switch JoyCon and Bosch electric hand drill – are shown below. The mass error was less than 1g for each of these parts, and the centre of mass position error less than 1 mm (averaged).
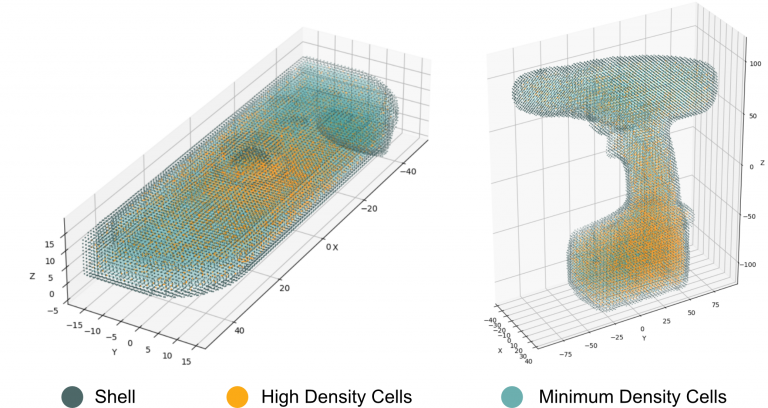
This work is currently being written up for a journal paper. Check back soon for updates on publication and further developments.