by David Jones and Owen Freeman Gebler
As part of the ProtoTwinning project (https://gow.epsrc.ukri.org/NGBOViewGrant.aspx?GrantRef=EP/R032696/1), we are evaluating metrology methods for digitally capturing evolving prototypes.
We are currently experimenting with the Einscan Pro+ (https://www.einscan.com/handheld-scanner/einscan-pro-plus/), photogrammetry using Agisoft MetaShape (https://www.agisoft.com/), and the FARO Arm (https://www.faro.com/en-gb/products/). It’s early days but see below for where we are.
Einscan Pro+
The Einscan Pro+ is a structured light scanner from Shining3D. A key challenge to metrology is controlling environmental variables such to minimise noise in the scans. Our solution is the black box rig that contains the scanner and turntable. We can now repeatably scan with no noise!
Next steps: Shining 3D are releasing a new version of their software, once we have a copy, we’ll complete our evaluation.
The all new Einscan Rig An example of the Einscan output – a virtual copy of a phone stand
Photogrammetry (with Agisoft MetaShape)
Photogrametry has seen some big developments in recent years. It involves taking multiple pictures of an artefact and then digitally identifying features within and across each photograph and transforming those features into point clouds. It sounds complicated but Agisoft MetaShape does all the hard work. See below for a measurement taken from both the physical artefact and virtual meshed copy. Again it’s early days but results are looking promising.
Next steps: photogrametry rig! Similarly to the Einscan, controlling the environment can improve the quality of both the photographs and so the final virtual model. We’re currently experimenting with taking photographs through a glass base to obtain full 360 degree coverage of the artefact.
Physical artefact – cutout measured as 11.72 mm The virtual copy of the artefact – cutout measured as 11.7175 mm
FARO Arm
The FARO Arm is by far the most accurate measuring device we’ve looked at so far. See below for an example of a sampled point cloud.
Next steps: with the high degree of accuracy comes massively dense point clouds that require a lot of processing power to mesh. We’re looking at optimal sampling methods to reduce the number of points (such that the scan is usable) while generating a high detailed mesh.
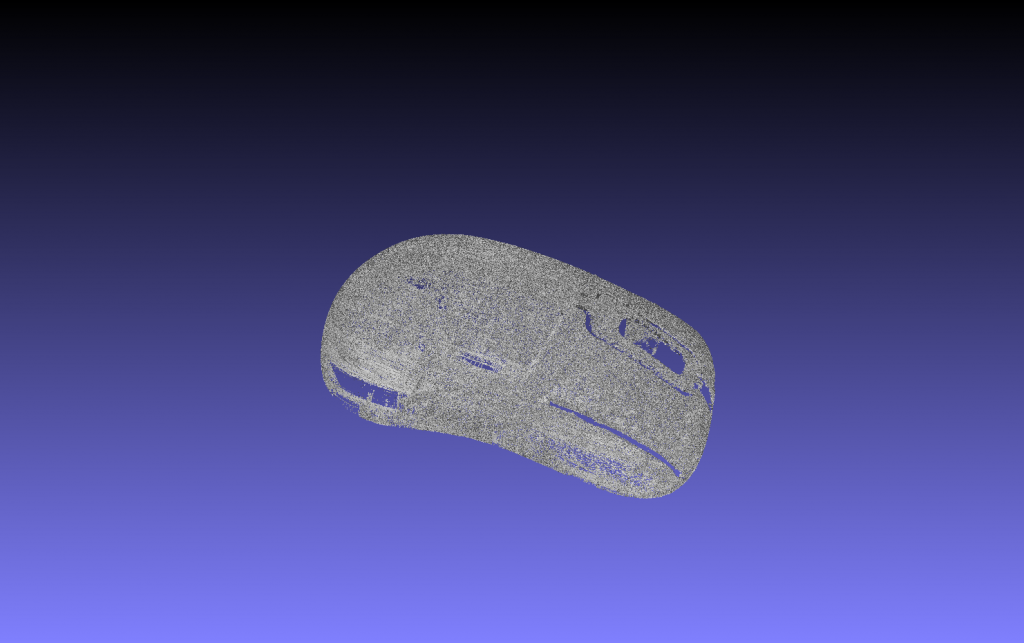
Where’s all this going?
The end goal of this specific piece of work is to use each method to measure a range of primitive shapes and generating a ‘best practice’ process for each technology. Once we have this, we’ll be using these technologies to capture how prototypes change during real prototyping activities, to better understand change in prototyping. Why? Our ultimate goal is revision control for physical prototypes. Once we understand how prototypes change, we can better design an approach to structure the revision process, bringing the benefits of software revision control to physical artefacts. Watch this space…
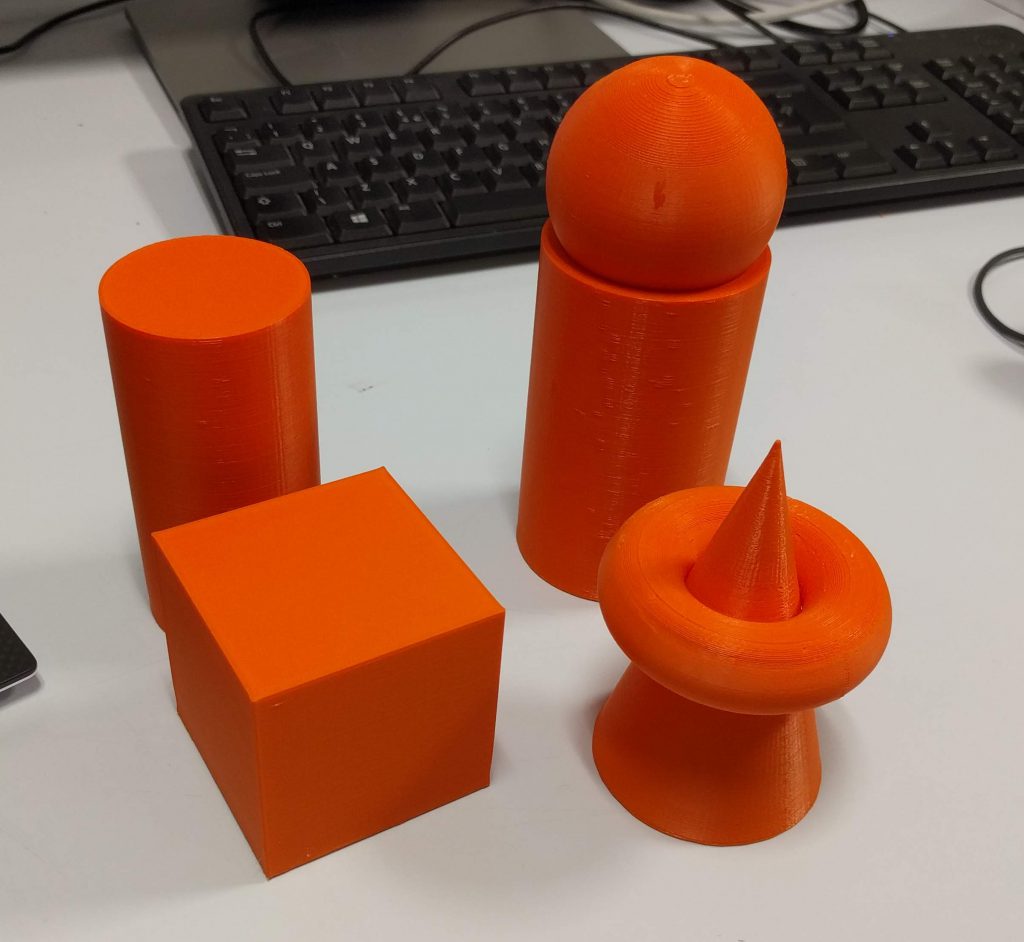