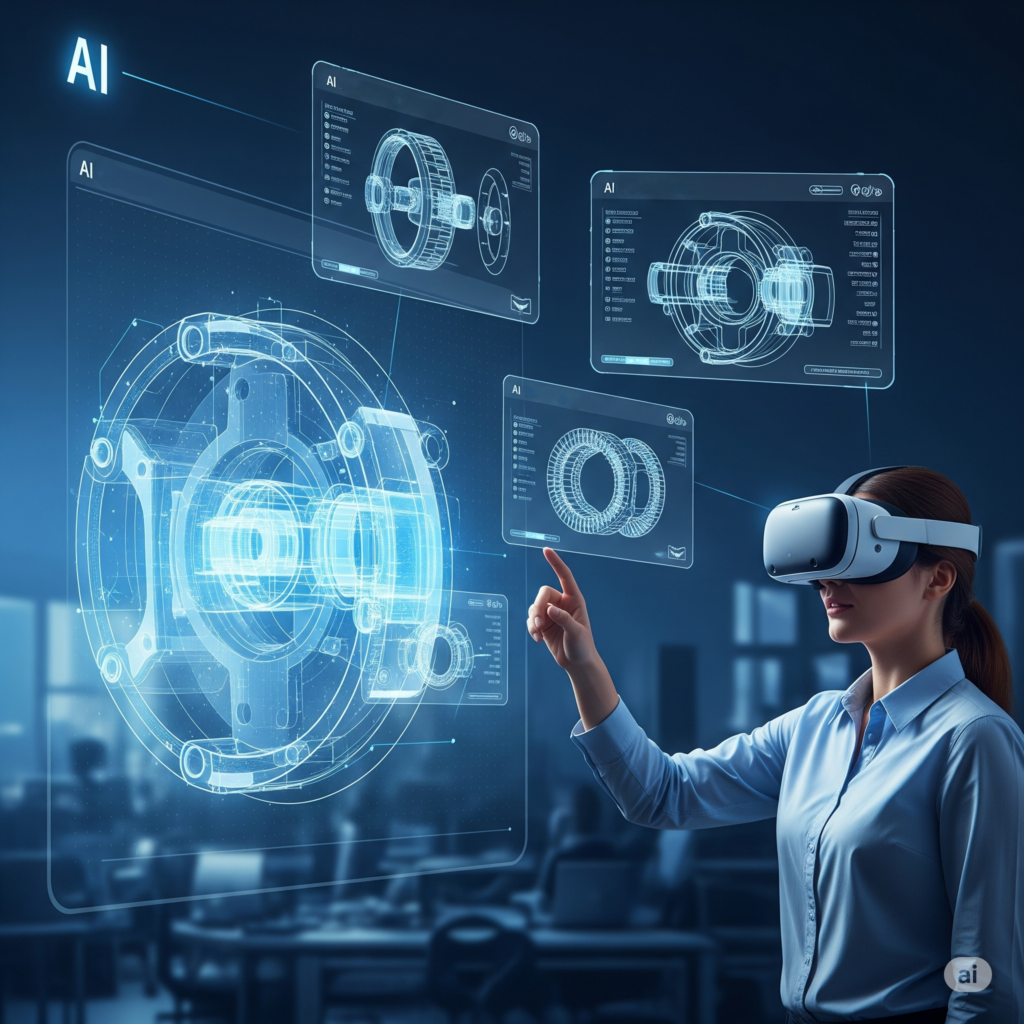
Ability to design engineering models in an immersive 3D space opens up completely new possibilities to design faster, better, and with less. One can interact with the design as if it was right in front of them, making adjustments with natural movements, and seeing the results instantly.
In our research group, we’re incredibly excited about the potential that Virtual Reality (VR) holds across design and prototyping workflows. VR is being increasingly used for design reviews, stakeholder collaboration, and even initial modelling. It promises faster design cycles, more effective product designers, and an intuitive, spatially aware environment that fosters creativity.
The Current Hurdle: From Art to Engineering Precision
However, when it comes to creating precise, usable engineering models, VR-CAD still faces a significant challenge. Most current VR-CAD solutions, often built on game engines, produce mesh-based models. Whereas traditional engineering CAD relies on a parametric data structure, allowing for exact control over dimensions and relationships. Mesh models lack the underlying structure needed for subsequent modifications during the design lifecycle and downstream applications like stress analysis or computer-aided manufacturing.
Many existing VR-CAD tools either focus on artistic design or simply try to replicate conventional 2D CAD interfaces in VR. While familiar, this approach often falls short because humans, in spatial environments, are inherently imprecise. Imagine trying to select a tiny endpoint or control complex operations with perfect accuracy in VR – it can lead to information overload and a frustrating lack of precision.
Our Solution: Integrating AI and VR for Parametric CAD
We, at DMF lab, have developed an integrated AI-VR system to overcome these very limitations. Our research delves into a novel approach that doesn’t just put CAD in VR, but fundamentally rethinks how we interact with design in a virtual space.
This system can:
- Convert intuitive VR inputs into precise CAD formats.
- Understand and translate imprecise human movements into accurate, purposeful parametric CAD commands and thus features.
- Provide an intuitive VR-CAD interface that avoids information overload, truly leveraging the benefits of virtual reality without sacrificing precision.
Our system integrates a VR interface with a CAD kernel and a machine learning (ML) that recognises users’ intentions. This unique combination allows for the seamless creation of parametric CAD models through natural, intuitive inputs in VR.
A Sneak Peek!
We’re incredibly excited about the potential this integrated system holds for the future of design and engineering.
The video below shows our working system that shows the creation of design features by intuitively carving out material that is then recognised by an AI model to regenerate a parametric model in real time.
The image below shows the model created in VR and its parametric model automatically generated using the developed toolchain.
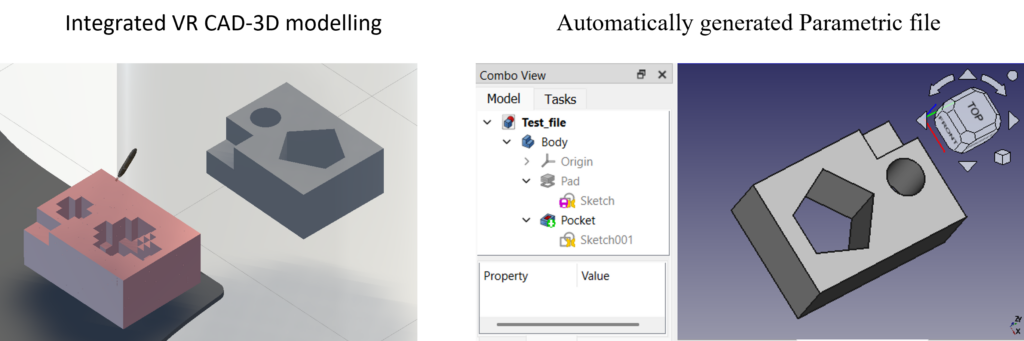
What’s Next?
We have increased computational efficiency to cater to much higher resolutions and give users more control over feature carving, and we are building other intelligent design tools. The developed application can now handle over 10 million voxels without lag and would significantly improve recognition accuracy (test) from 89% to >98%.
This development gives exciting opportunities for the future of engineering design. It opens the door to integrating various other logics and models to work together and expedite the design process. For example, LLMs can be integrated to help refine the designed features and add dimensions, design for manufacturing constraints can be included, or even low-fi FEM simulations can be performed on designed prototypes for more informed design.
AI integration with VR could be the KEY that can bring VR-CAD to the forefront of Engineering Design. What are your thoughts on the future of VR in design? Let’s connect and discuss!