Is Seeing Believing? Investigating the influence and interplay of physical and virtual traits on the user perception of Mixed Reality prototypes.
There is a significant drive in Design Research towards creating realistic prototypes for without requiring significant time and funds.
Mixed Reality (MR) prototyping may offer a solution to this requirement. New research, due for publication in Design Science, explores how MR prototypes can be used in product design, and how the virtual and physical domains can be blended to maximise value.
Traditionally, creating prototypes can be a costly and time-consuming endeavour. MR offers an interesting middle ground, merging physical and virtual elements to gain the benefits of both domains. This particular study investigated how users perceive the fidelity of MR prototypes, specifically focusing on the interplay between the physical and virtual aspects.
The researchers conducted an experiment where participants interacted with MR prototypes of a cordless drill. These prototypes had variations in both the virtual and physical size and mass. After interacting with each prototype, participants were asked to gauge how realistic it felt, and give their impression of the prototype and how it differed from the previous iteration.
From this, we found that the changes made to the virtual (visually perceived) size of the drill had a far greater impact on how participants perceived the prototypes, compared to changes in physical size. Interestingly, there also seemed to be some flexibility with the physical aspect. Even a significant difference (70%) between the virtual and physical size of the drill didn’t significantly affect how real it felt to participants, and the virtual perception ruled the overall perception.
Furthermore, as long as the physical mass of the prototype was “within reasonable bounds” (i.e. not a plain, unweighted 3D printed model) the prototype felt like a real drill in the participant’s hand.
So, what does this mean for designers? When creating MR prototypes, virtual elements should be prioritised. High-quality visuals with accurate colouring, textures, and lighting are key. The physical component can be less detailed, as long as it has a realistic weight, sufficiently accurate geometry, and allows users to interact with the crucial features. This approach has the potential to save significant time and money compared to traditional prototyping methods.
This research is just the first step. The study focused on a single product, and further work is needed to see if these results hold true for other types of products. The desire for interactive features in the virtual world highlights another exciting avenue for exploration. By understanding how to effectively leverage both the physical and virtual aspects of MR, designers can unlock a powerful new tool for creating low-cost, high-fidelity prototypes. This could accelerate the design process and ultimately lead to better products reaching the market faster.
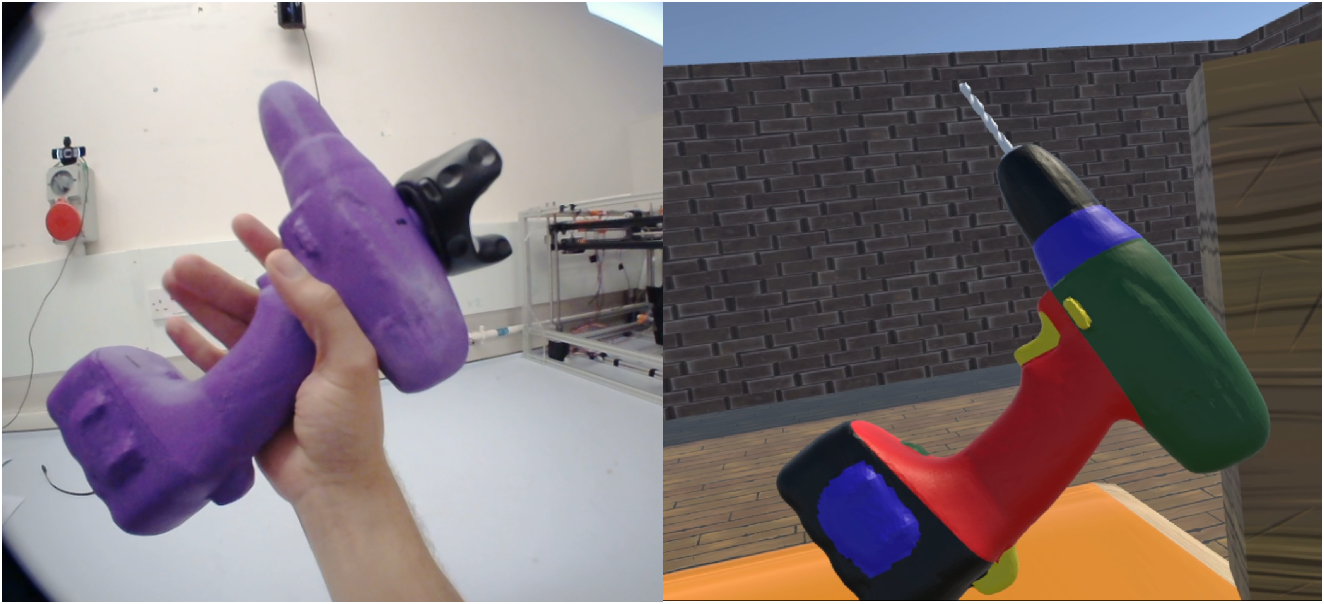
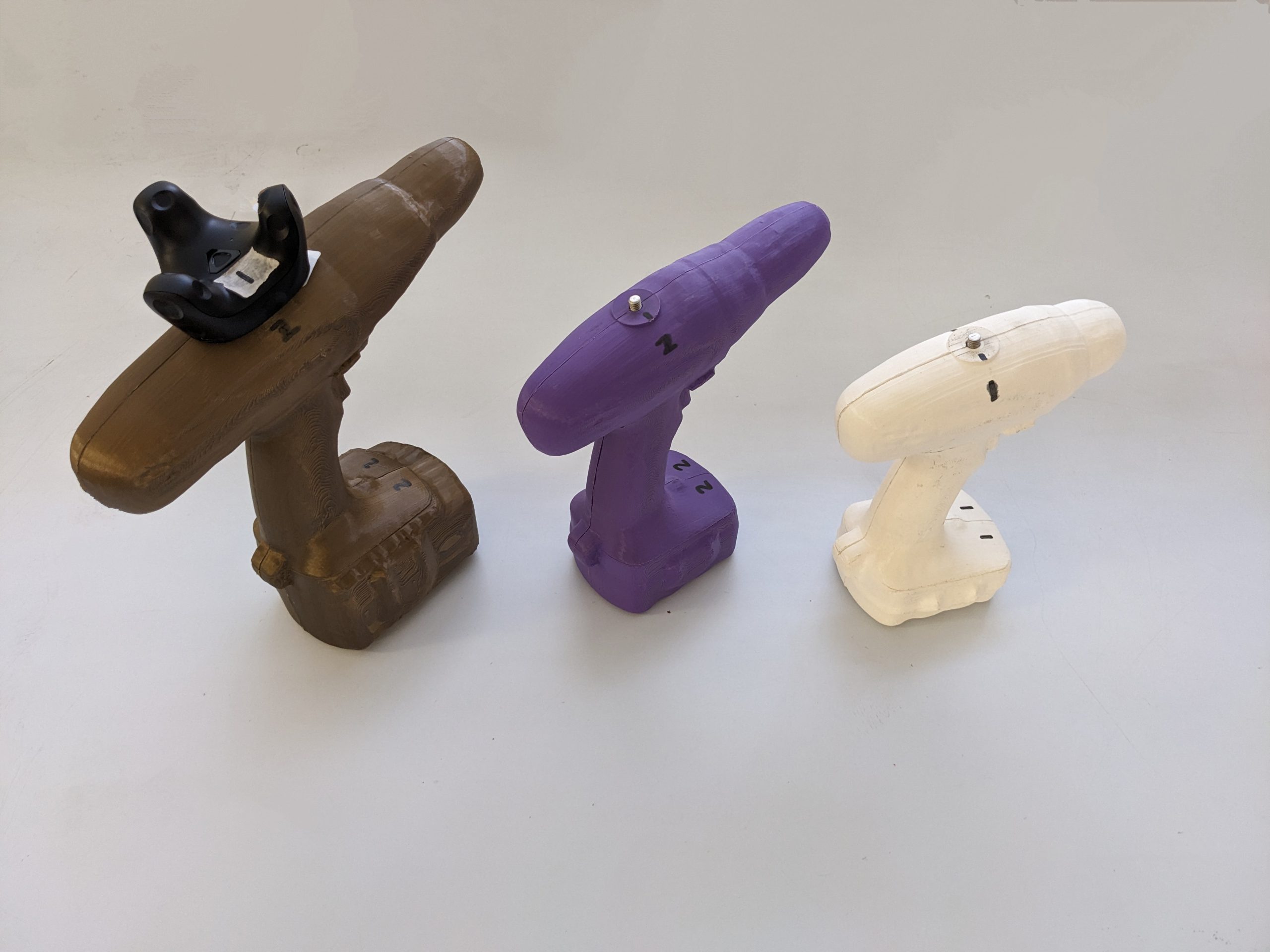
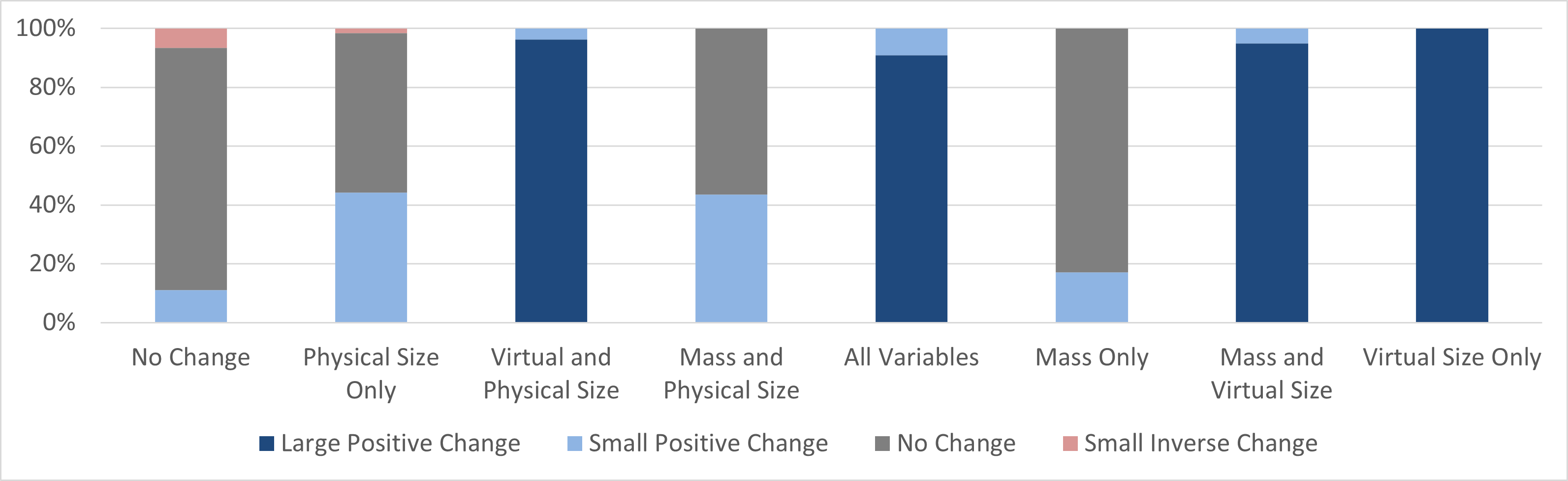